Cooling Tower Replacement – Ultima Tower Case Study
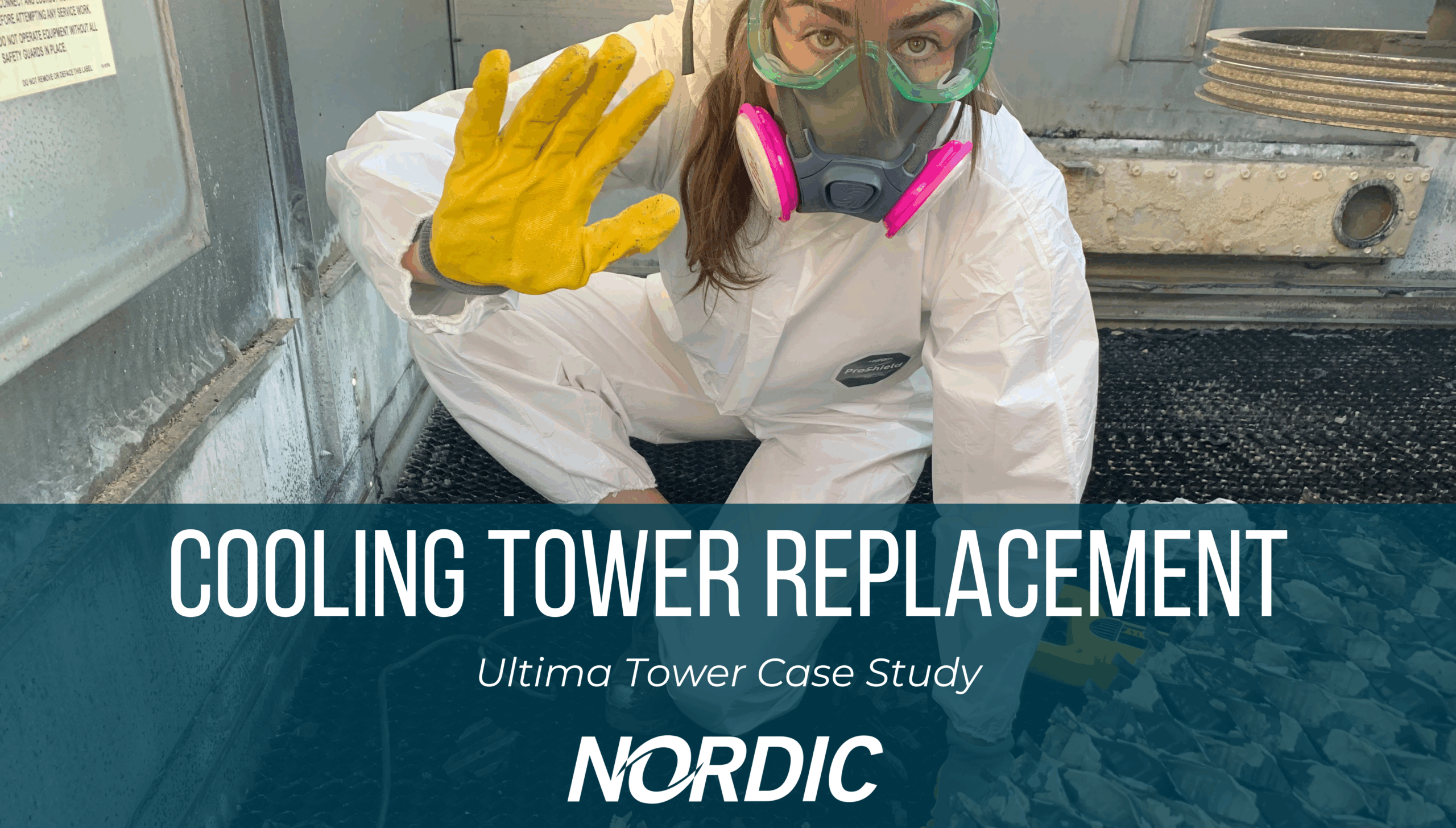
When it comes to HVAC systems, preventative maintenance is crucial in ensuring longevity, efficiency, and cost-effectiveness. This case study highlights a cooling tower project where a lack of maintenance led to premature equipment failure, high repair costs, and discomfort for the building’s occupants.
The Challenge
Built in 2016, this facility’s HVAC system was already facing severe operational issues, requiring major repairs and replacements. The primary problems included:
- High emergency repair costs due to equipment failure, with cooling tower repairs typically ranging from $15,000-$30,000.
- Significant heating and cooling inefficiencies.
- A completely clogged heat exchanger.
- A severely calcified, broken, and deteriorating cooling tower fill, which was no longer distributing water effectively.
- A lack of water treatment, leading to bacterial growth, corrosion, and sludge buildup in the system.
Without proper maintenance and water treatment, the facility’s HVAC system was operating inefficiently, leading to increased energy costs, equipment deterioration, and an uncomfortable indoor environment.
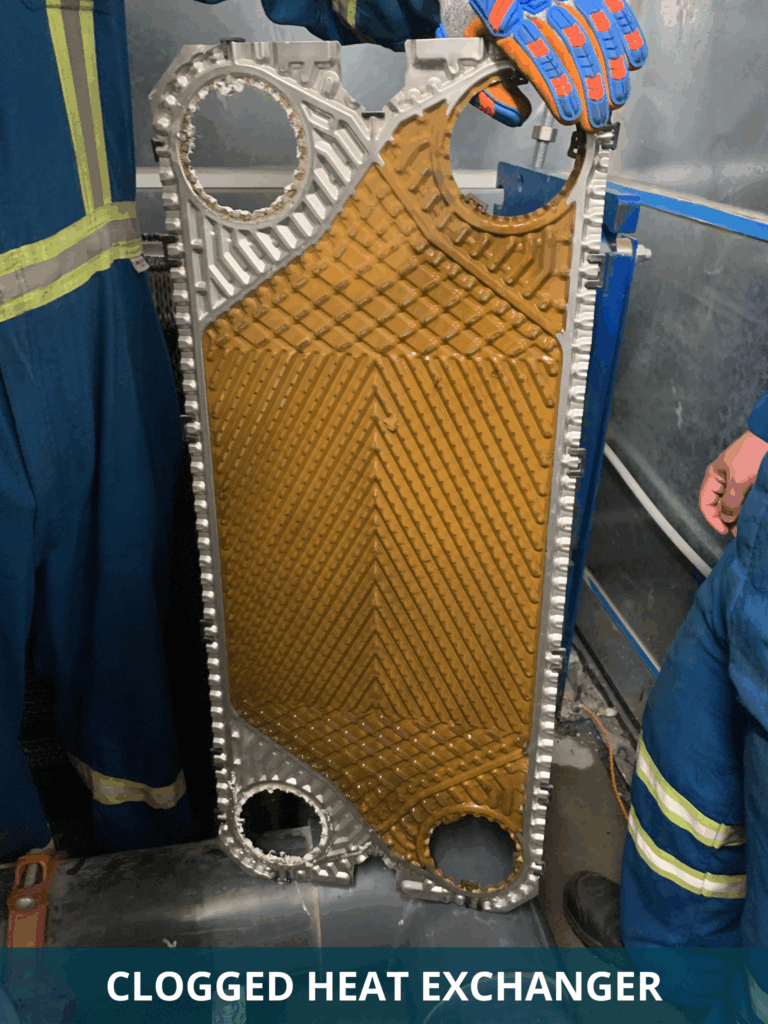
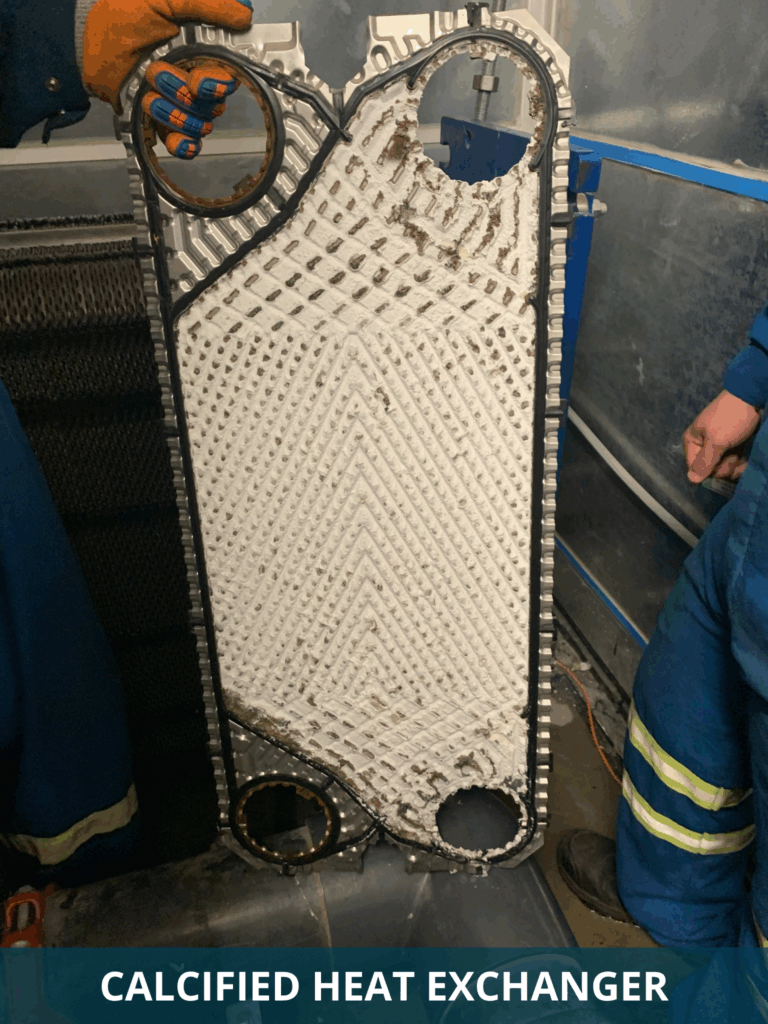
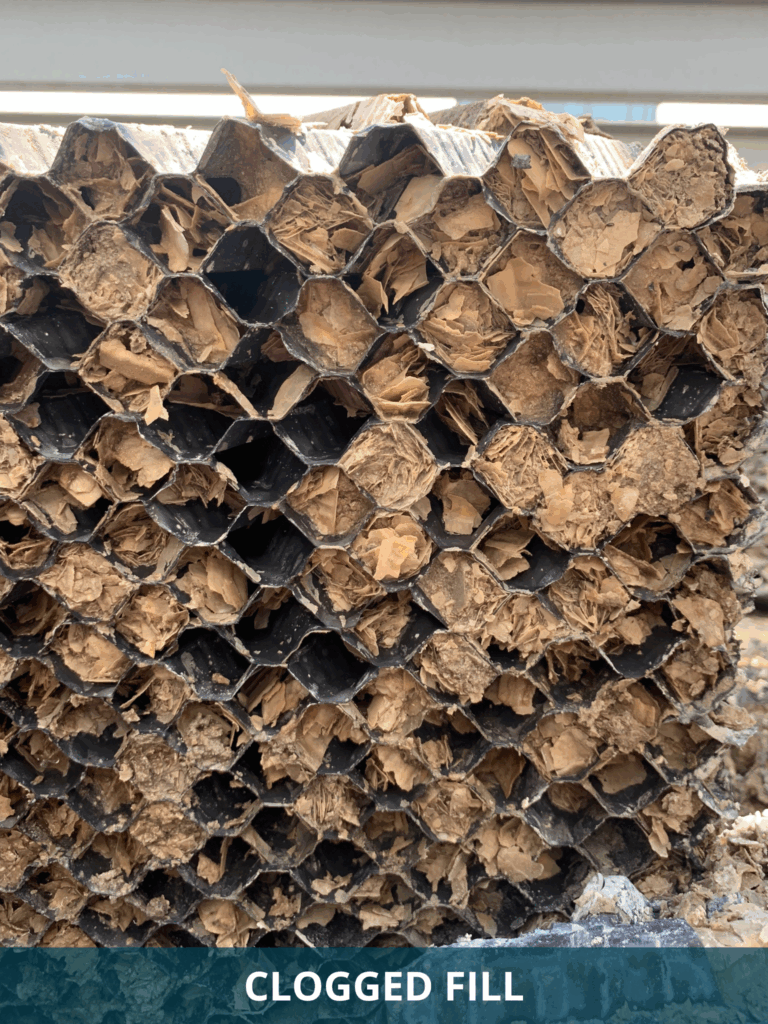
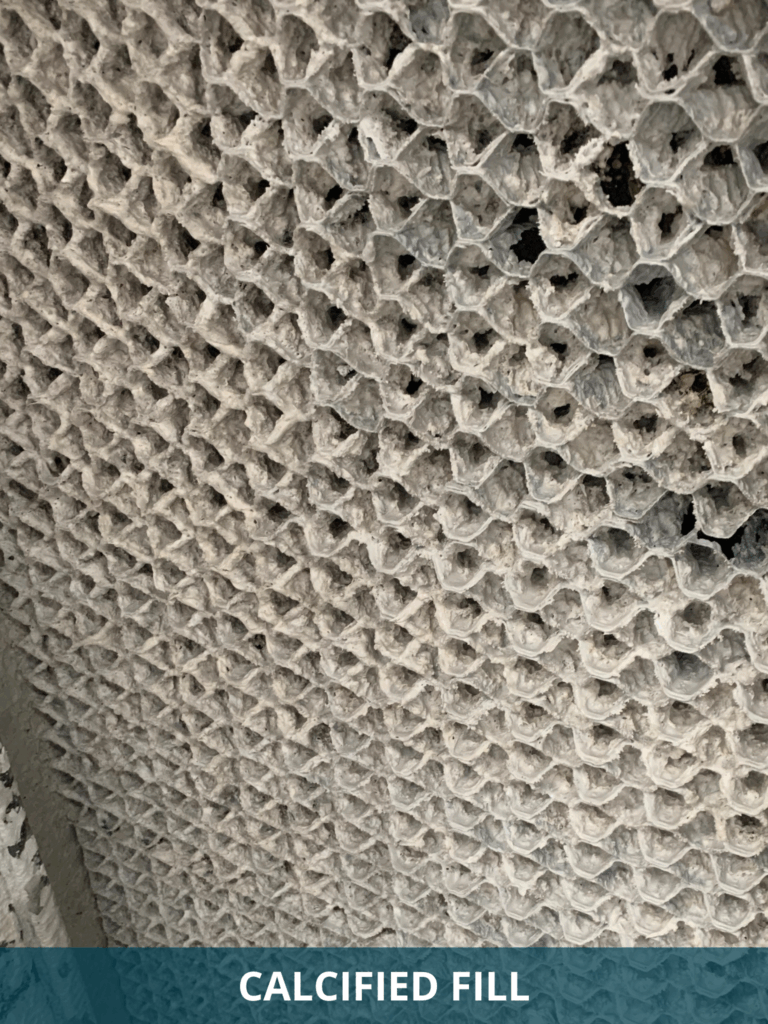
Our Solution
To restore functionality and prevent future failures, we executed a comprehensive rebuild and maintenance plan:
Cooling Tower and Heat Exchanger Restoration
- Cleaned the tower sump, strainers, and drained the cooling tower loop, which was filled with thick sludge due to years of untreated water.
- Rebuilt the completely clogged heat exchanger, which had become blocked by debris and buildup, restricting proper heat transfer and system efficiency.
- Installed a new fill to restore proper water distribution and tower performance.
Water Treatment Implementation
- Introduced a comprehensive water treatment plan including filtration technology and chemical/biocide dosing to eliminate bacteria, reduce total dissolved solids (TDS), and prevent corrosion.
- Implemented chemical and biocide treatment to prevent bacteria, scaling, and corrosion.
- Established an ongoing water treatment schedule and monitoring to ensure consistent chemical balance and equipment protection.
Preventative Maintenance Plan
- Implemented a preventative maintenance agreement including regular inspections, water treatment monitoring, and system checks.
The Results
Thanks to the repairs and the introduction of a preventative maintenance plan, we achieved the following results:
- Immediate improvement in cooling efficiency, reducing system temperature from 47°C to 25°C.
- Significant savings on energy and water costs.
- Lowered operating expenses by eliminating emergency repairs.
- Restored comfort for residents and building occupants.
- Prevented future system failures through scheduled maintenance and water treatment.
Why Preventative Maintenance Matters
This project highlights the importance of regular HVAC maintenance. A well-maintained cooling tower extends equipment lifespan, reduces costly repairs, and ensures energy efficiency. By implementing a proactive maintenance plan, businesses can avoid expensive breakdowns, improve system performance, and provide a comfortable environment for occupants.
Contact us today to learn more about our preventative maintenance programs and how they can save you money while ensuring reliable HVAC performance.